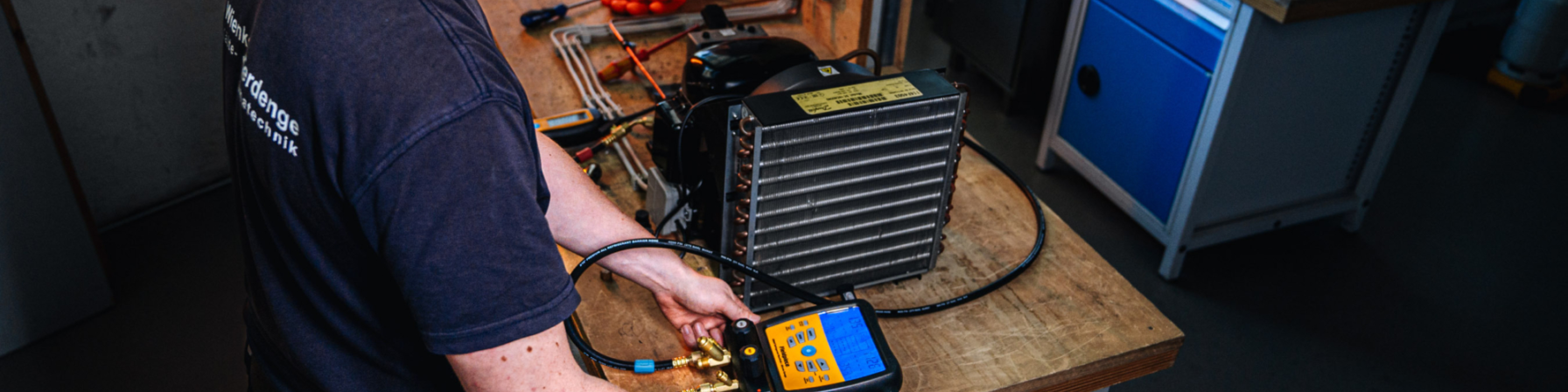
Tips for Technicians
Ever been stuck on a tough repair or spent way too long figuring out a system issue? We’ve all been there. This new blog series is packed with practical advice, smart solutions, and hands-on tips you can immediately use to solve problems faster and work smarter. No fluff—just the information that makes a difference when you're out in the field.
Challenges in the Field
In the previous blog in the Tips for Technician series, we looked at how to systematically approach a troubleshooting job. This included steps like making sure the power is working, measuring the temperature around the lines, and checking the refrigerant charge for example. This blog also briefly mentioned the importance of your compressor in the system you’re troubleshooting. This week, we’ll dive in further to understand why the compressor can play a significant role in your troubleshooting process.

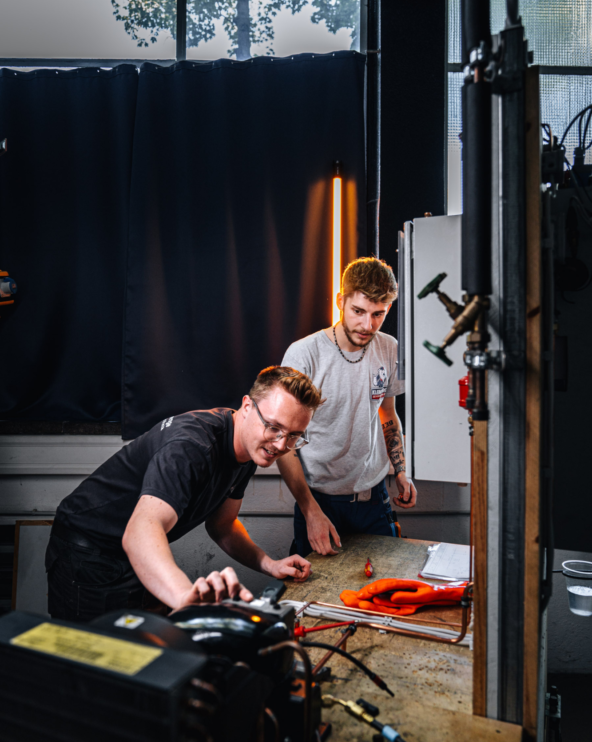

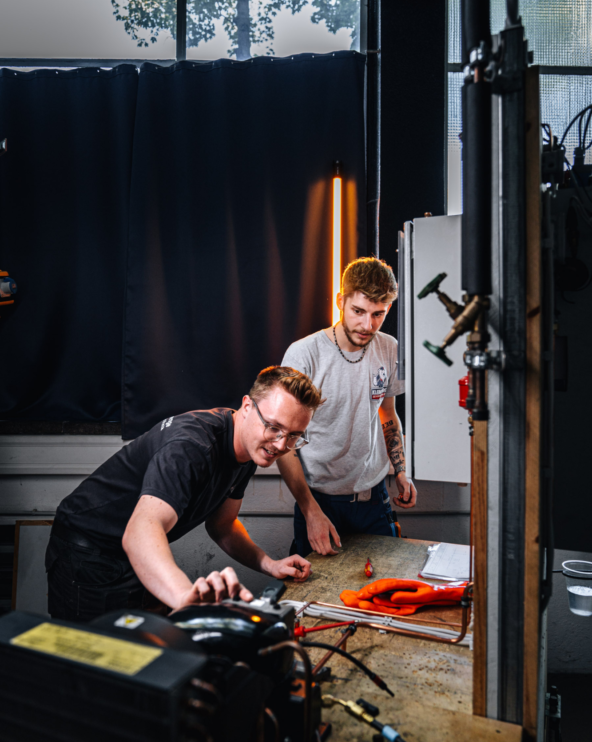
If you find yourself at a job where the compressor is the failing component of the system, it is highly important to not just replace the compressor and ‘finish the job’. To build customer trust, and reduce callbacks, it is essential to find out why the compressor was failing in the first place. Simply replacing the compressor and walking away often won’t fix the issue in the long-term.
A compressor in an HVACR system can fail for several reasons, many of which come down to refrigerant issues, faulty expansion valves, or improper system setup. One of the most important checks is the refrigerant charge—too much or too little can cause faulty operation and increased stress on the compressor. Overcharging can lead to high pressures, while undercharging can cause overheating and oil return problems.
Ensuring the pipework is sized and installed correctly is also critical. Poorly calculated piping can result in pressure drops, oil trapping, and inefficient refrigerant flow, all of which can overwork the compressor and shorten its lifespan. Proper pipe sizing and layout help maintain system efficiency and prevent unnecessary strain on components.
Expansion valves, especially in VRF and VRV systems, are another common failure point. These motor-driven valves control refrigerant flow, and if they malfunction, they can allow liquid refrigerant to flood back to the compressor. Since compressors are designed to handle gas, liquid refrigerant can cause slugging, damage valves, and wash out lubrication, leading to severe mechanical failure.
What are VRF and VRV systems? Variable Refrigerant Flow (VRF) and Variable Refrigerant Volume (VRV) are two different terms for the same type of system. VRF/VRV systems rely on refrigerant as the primary heating or cooling source. These systems also use inverter compressors, which means the compressor is able to run at different speeds to save energy. The terms VRF and VRV are both used to describe the same type of system, but the name VRV is trademarked by Daikin Industries.
Another key factor is the compressor heater, often called a crankcase heater. If it’s not working, the compressor won’t properly warm up before startup, increasing the risk of mechanical failure due to cold oil and improper refrigerant flow. Checking that the crankcase heater is operating as it should, can prevent premature wear and costly breakdowns.
Finally, it’s important to remember that the compressor is more than just a part of the HVACR system—it’s a critical component that can indicate underlying issues when it fails. By understanding the factors that contribute to compressor failure, like improper refrigerant charge, valve malfunctions, and system setup issues, you can troubleshoot more effectively and avoid unnecessary replacements. A successful repair isn’t just about replacing the compressor—it’s about finding the root of the issue to prevent future problems. By taking your time to find the underlying issues, you’ll not only fix the immediate problem but also help ensure the system runs smoothly for the long haul, saving both you and your customers time and money.
Stay tuned for the next part of the Tips for Technicians blog!

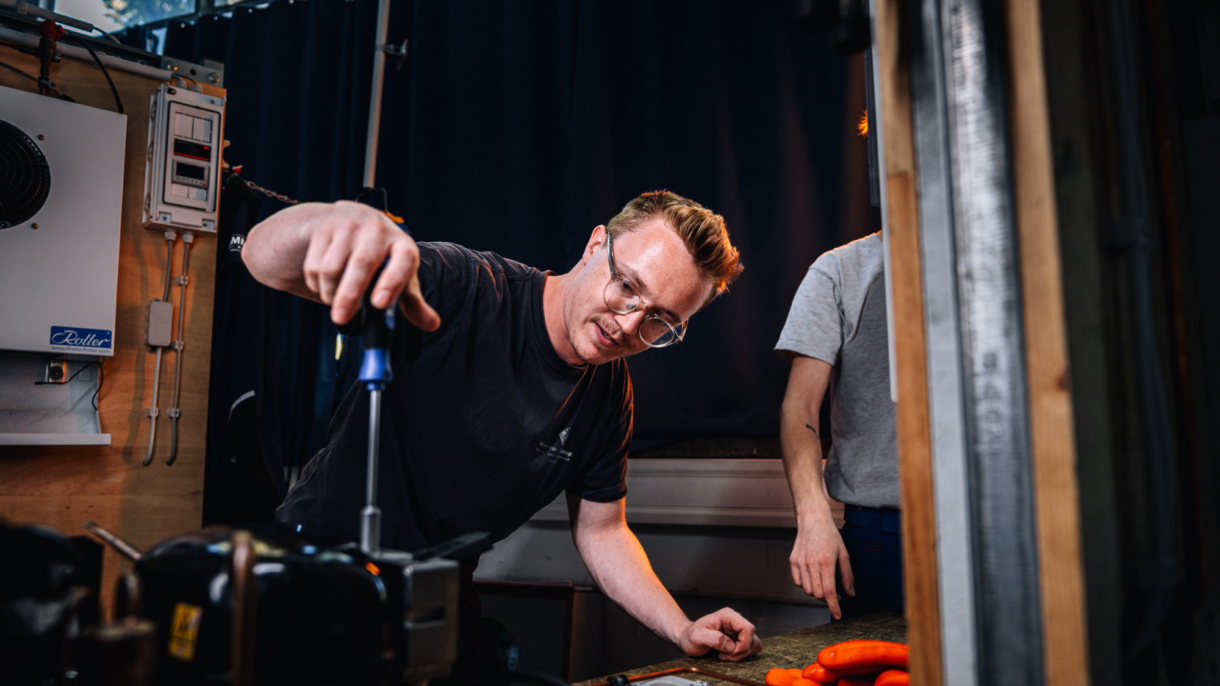